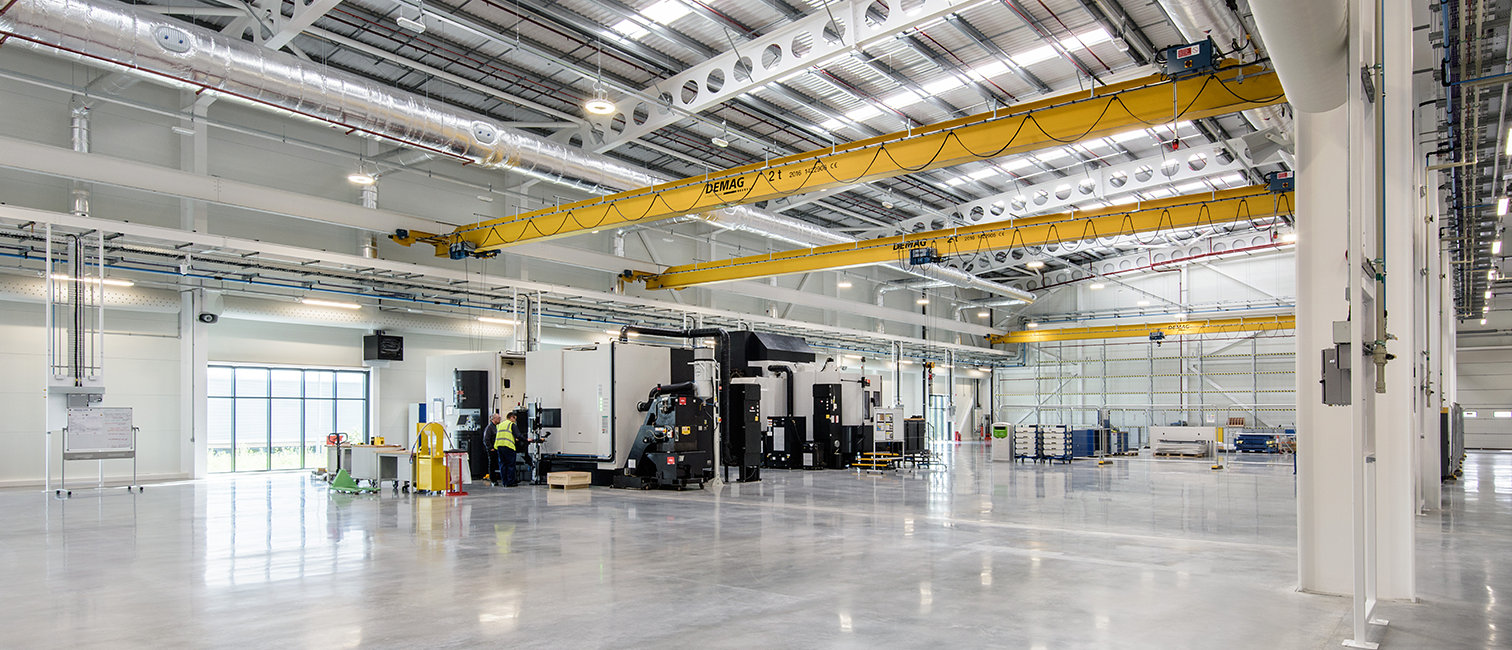
Client
Rolls-Royce
Value
£18,300,000
Architect
Maber
Duration
55 weeks
Design and construction of a new aero engine disc manufacturing facility of 72,118 sqft.
Design and construction of a Rolls-Royce aero engine disc manufacturing facility of 72,118 sqft at the Washington site which uses advanced manufacturing techniques to produce high-tech aero engine components. The new facility can manufacture over 1,500 fan and turbine discs a year for use in a wide range of existing engines, including Civil Aerospace and Defence Aerospace applications. The contract was split into two phases. Section 1 involved the design and build of the main manufacturing hall with eight overhead cranes, heavy RC slab and broach pits.
Further works included the construction of the CMM (Coordinate Measuring Machines) clean rooms, offices, ancillary areas and external works involving roads, plant areas, landscaping and designated areas for deliveries and distribution by large vehicles. Phase two required McLaughlin & Harvey to remain as the principal contractor for the fit-out process which included management, attendance and coordination of equipment suppliers and fitting out of specialist production equipment post-completion.
New
Manufacturing
Facility
The project was complex due to the design of the building and the internal services to cater for the client’s internal processes. Early in the programme, we identified the condition of the ground solutions which had been worsened by the previous contractor on the site. However, through the two-stage tender process, we presented four options of piling to Rolls-Royce who assessed the risks to their adjacent CMM rooms, situated no more than 20m away from the new facility. The CFA piling solution was chosen to minimise the risk of vibration and interference with their current site processes. We also had to design the solution around the new CMM room which had to be a fully isolated slab structure.
The project was the first Rolls-Royce had been involved with which was delivered on time and budget. It was also approved on the first visit by the Civil Aviation Authority and won second place in the global Rolls-Royce project awards.